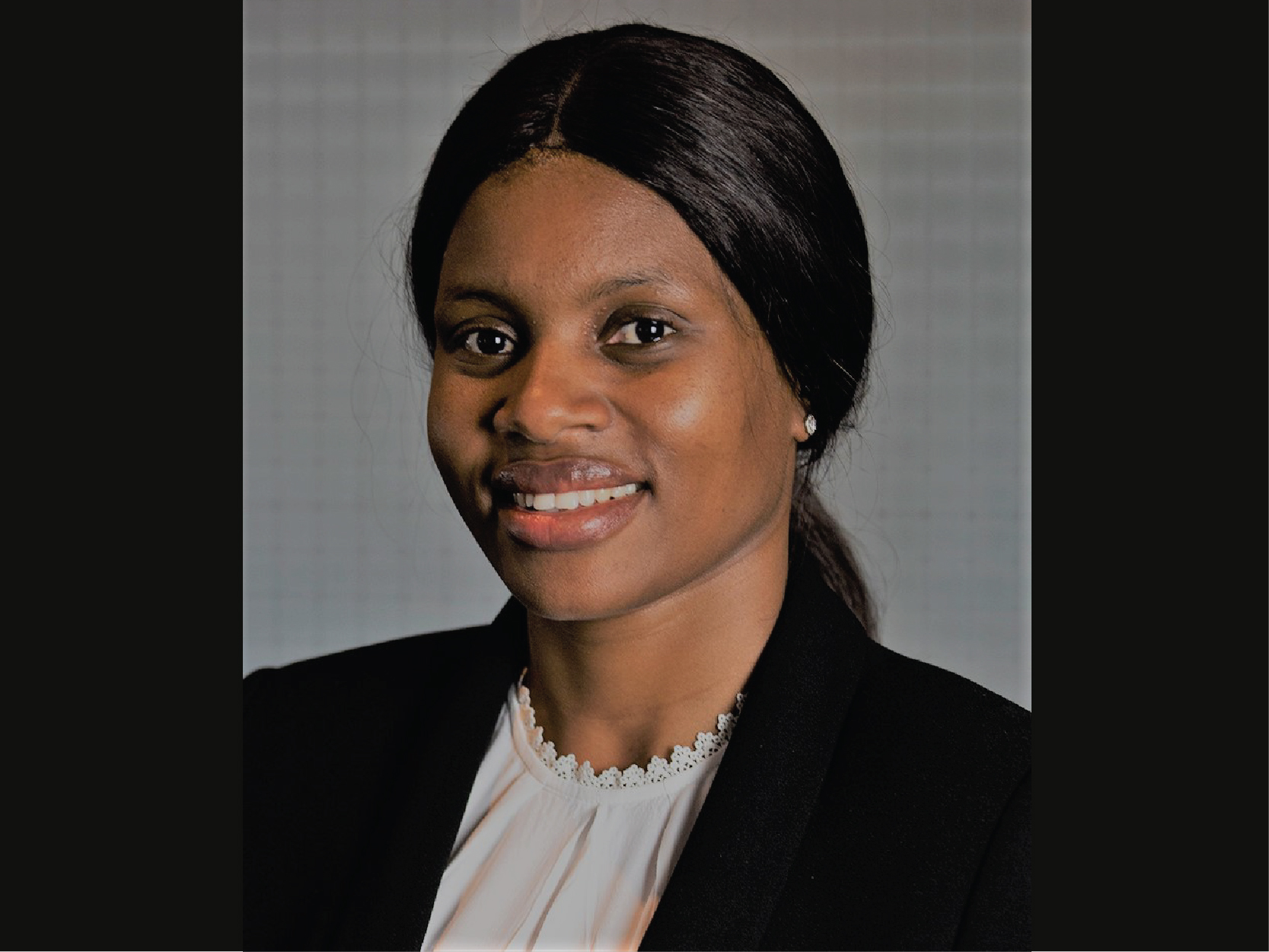
UMS RETURNS TO ITS ROOTS WITH LOCAL PROJECTS
Rob Hull, COO of UMS, says that although the company has secured significant international projects over the last few years, it always had its sights set on more local work. “While we serve global mining and minerals processing clients, our origins are in the South African mining sector. We have been involved in many of the major underground developments in South Africa and have a deeply experienced team who have an intimate knowledge of local mines.
“This, together with the lessons learnt in the last few years, a drive to incorporate innovation to improve safety and efficiencies, and a strong focus on skills transfer have all contributed to UMS securing a number of local projects, including the prestigious Sedibelo Resources Limited Triple Crown decline shaft project,” says Hull.
Sedibelo Resources (SRL) on the Western Limb near the Pilanesberg platinum mine concentrator has engaged UMS for the development of their underground project, which represents a diversification from their current opencast operations.
SRL’s platinum assets are situated on both the Western and Eastern Limbs of the Bushveld Complex, which contain circa 90% of the world’s known reserves of PGMs.
UMS’s scope of work includes decline development, raiseboring and underground development, to be executed in four legs over a five-year period. Takalani Randima, MD of UMS Shaft Sinking, elaborates on this and says that UMS will be involved in the drilling and blasting of the main, conveyor belt and service declines, constructing the anchor support, shotcreting, blasting for workshops, and constructing the ventilation and ore passes. UMS will be raiseboring between each leg for an optimal ventilation system.
Randima explains that as the underground ore body in this region is relatively shallow, the decline slope is just 9 degrees, with the reef at a depth of approximately 620m below surface, allowing for mechanised equipment to be used such as drill rigs, dump trucks and utility vehicles. It will also allow the client to contemplate the use of electric and battery vehicles at the levels development stage.
“Safety is a critical factor in delivering this project,” says Randima. “Historically SRL has a top-quartile safety record, and our team is working closely with the head office and the client to ensure that a number of safety measures are implemented to prevent any harm to persons and machinery.
“Furthermore, UMS is committed to meeting project targets and milestones, which has not always been the case in underground development projects.”
Another critical factor to project success is UMS’s approach to CSI projects. “We have a thorough CSI plan, coordinated with the client, which will be a key component of how we develop and deliver this project,” says Hull. “Besides bringing our technical expertise in mining development, we are prioritising sustainability for the community by offering training and thereby creating a pool of skilled and trained community members for the mines to recruit from.”
One of UMS’s key training objectives is to ensure that local employees are fully trained in trackless mobile machinery (TMM) as operators, artisans and qualified TMM miners by the time UMS’s five-year scope of work is completed. As such, UMS will be contributing to the sustainability of the community by focusing on training artisans and transferring skills in association with other training operators and OEMs.
While the company is proud to be part of SRL’s Triple Crown project, one the most significant mining development projects in South Africa in recent times, Randima adds that UMS is also committed to solving mining clients’ smaller and yet complex challenges. In recent months, UMS has been involved in a number of mine shaft rehabilitation projects, including at a manganese mine in the northern Cape, a platinum mine near Rustenburg, and most recently, the Kusasalethu gold mine in Gauteng.
For the Kusasalethu project, she explains that UMS is currently rehabilitating an upcast shaft at the mine that is used as an emergency escape route. The aged shaft steelwork has to be replaced and UMS was tasked to come up with a solution to access the steelwork along the shaft walls safely.
“The challenge with this shaft is that it has two cages that operate on a pulley system, so any movement on one cage will affect the other cage. UMS’s design division, UMS METS, designed a skeleton to be fitted underneath the cages that could be opened up and used safely on both areas simultaneously as opposed to other skeletons that can only be used on one section at a time,” explains Randima.
“What is also interesting about this five-month project is that since it is an upcast shaft through which air escapes the mine, UMS can only work during day shifts because the client blasts in the afternoon. When UMS is working in the shaft, the underground booster fans have to be switched off. This means we have to work quickly and efficiently without compromising safety, and this is where our experience and knowledge of existing shaft infrastructure, combined with new shaft technology, really comes to the fore.
“We have a range of skills and an in-house team with the expertise and ability to solve our clients’ challenges swiftly and safely, whether it’s a five-month or five-year contract. We understand what is required, and can mobilise quickly regardless of the size or scope of the project,” concludes Randima.