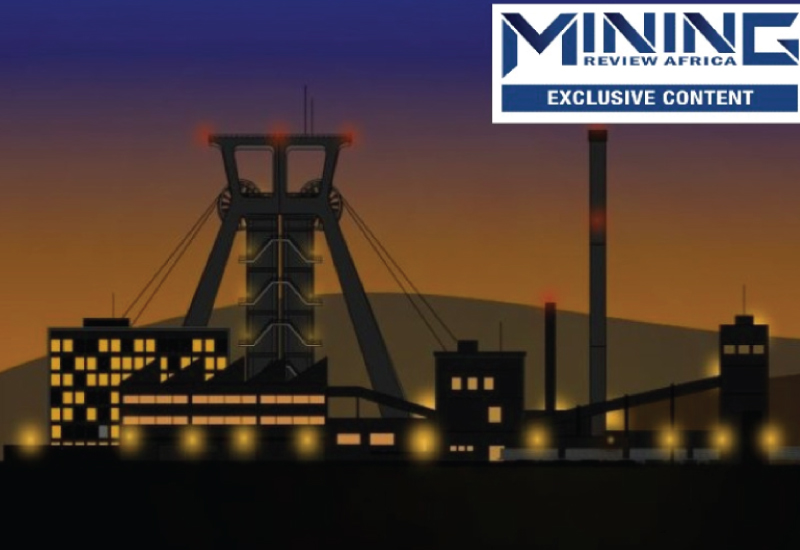
UNDERGROUND MINING: AIMING FOR PERFECT HARMONY
Underground mines (particularly deep level mines) have always posed the greatest risks to safety, especially in South Africa which has been mining some of the deepest ore bodies in the world for decades. Traditionally, the greatest number of fatalities have occurred in these mines – from shaft sinking through to development and mining.
“South Africa’s poor safety performance has been in the spotlight for the last decade or two and has remained there ever since. Government, mining houses and contractors have all implemented a zero-tolerance policy for unsafe mining practices and the industry has responded, looking at technologies and methodologies to protect its workforce, at all costs,” says Dr Pieter Louw, group executive: project services at UMS Group – a South African based company that specialises in shaft sinking and underground mining development and operations.
“South Africa’s safety performance has really been the dominant focus and the results can be seen. However, in some instances, this has resulted in new thinking and creative ways to look to ensure we remain productive,” continues Murray Macnab, group technical director at UMS Group.
“While we are still driving towards a zero-harm future, we do need to find a comfortable balance between mining safely and productively, finding and using technologies that achieve both,” he adds.
It is this scenario that paints the period of transition picture – the need to reach optimal levels of performance in both safety and productivity. A cactus grab for example is considered highly unsafe. With +40 people working in the shaft bottom simultaneously, fatalities were a given. Now that the cactus grab can be operated with no people in the shaft bottom, and no activities undertaken in parallel, then productivity can be elevated without compromising safety.
“The geology and economics of mines, especially in developing nations, do not always lend themselves to using methods like VBMs to sink shafts. Traditional blind sink activities, which include use of the cactus grab, will continue to play an important role in shaft sinking for many more years. Having re-engineered the way more traditional equipment is used, through innovative mechanisation and automation, means we can sink safely and without unduly compromising productivity,” Macnab outlines.
And while technology and methodology hold the key to achieving this, so too is the need for innovative people and industry thought leaders – who are prepared to challenge the status quo.
“Looking beyond shaft sinking, the greatest evolution within the underground mining space is mechanisation and some automation as well,” states Graham Roberts, MD: UMS Mets.
“The challenge has been and remains the fast-tracked approach to doing so. Often the need to chase production and reduce costs hampers investment in R&D in transitioning from older traditional mining practices to more modern mechanised and automated methods.”
However, a major shift in any industry is never without a few speed bumps, and learning how to address them starts with understanding what they are and talking openly and collectively. The South African mining sector is definitely working towards this and undoubtedly will find solutions.
“Fortunately, the younger generations joining the industry are proficient in the skills needed to work operations in a more mechanised and automated environment. They have grown up with gaming and so are familiar with remote control concepts. They are also not eager to undertake such hard and physical labour and are challenging traditional processes and practices – as such, they are in fact forcing the change we need,” Roberts highlights.
The big scare with mechanisation at present is also the reduction in workforces – but there is a bright light for employment at the end of this tunnel, says Macnab. “Mechanisation opens the door to create new employment – not on one specific mine per se but rather because it allows mines that have been economically unviable in the past to become viable – the more mines there are, the more job opportunities there are as well.”
Of course, the greater downstream effect of a bigger industry is greater opportunities for the industry’s support businesses – equipment supply, infrastructure, and even for communities that benefit from long-term sustainable livelihoods.
“So, we really need to drive the mechanisation approach and provide greater education on the opportunities it presents.”
The evolution of women in underground mining
There can be no doubt that there has been significant progress made with regard to employment opportunities for women in the underground mining sphere, says Takalani Randima, MD: UMS Shaft Sinkers.
“Mechanisation and automation technologies as mentioned remove the physical aspect of working in a mine and make it feasible for women to take on roles traditionally given to men. And this is only set to continue moving forward.”
There are however many challenges still to overcome – ablution facilities for example. “There are no toilets on the shaft sinking stage, and women therefore require extra time to return to surface and back to the stage which can be time consuming and disruptive. “The industry needs out of the box thinking to address such challenges,” Randima emphasises.
With the radical improvement in female numbers in the underground space, a solution to any challenge is bound to be solved, particularly with women such as Randima working in the field and putting in the ‘hard miles’ necessary to rise in position and gain respect from the industry.